Concrete is everywhere—it’s the backbone of our modern infrastructure, from highways and bridges to office buildings and homes. But have you ever wondered what happens to all that concrete when a structure is torn down? That’s where concrete crushing comes in.
Recycling concrete isn’t just about managing construction waste; it’s about turning what was once considered debris into a valuable resource. By breaking down old concrete into smaller, reusable pieces, you can create new materials for roads, foundations, and other projects—all while saving money and reducing your environmental footprint.
In this guide, we’ll explore the ins and outs of concrete crushing: what it is, why it matters, and how you can choose the right equipment for the job. Whether you’re a contractor, landscaper, or just curious about sustainable construction practices, this guide will equip you with everything you need to know to make concrete crushing work for you.
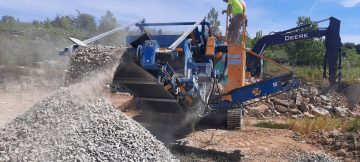
What Is Concrete Crushing?
Concrete crushing is the process of breaking down large pieces of concrete into smaller, more manageable fragments that can be repurposed for other construction projects. Instead of letting old concrete fill up landfills, crushing transforms it into valuable aggregates that can be reused for road base, drainage systems, or even new concrete mixes.
This process often involves specialized machinery, such as jaw crushers, impact crushers, or even hybrid models like the Rebel Crusher, which can handle a variety of materials. The goal is to produce uniform pieces of material that meet specific size and quality requirements.
Why Is Concrete Crushing Important?
- Waste Reduction: Instead of contributing to growing landfill volumes, crushed concrete can be recycled and given a new purpose.
- Resource Conservation: Recycling concrete reduces the demand for new raw materials like gravel, sand, and cement.
- Cost Efficiency: Crushed concrete is less expensive than new aggregates, saving money on material costs for construction projects.
By turning demolition debris into a usable product, concrete crushing is an innovative way to build more sustainably while cutting costs.
The Benefits of Crushing Concrete
Concrete crushing isn’t just a practical solution for managing demolition debris—it also offers a host of benefits for contractors, businesses, and the environment. Here’s why recycling concrete is a win-win for everyone involved:
1. Cost Savings
Recycled concrete is significantly cheaper than sourcing new materials like gravel or crushed stone. By crushing and reusing old concrete, you can save on:
- Material Costs: Crushed concrete can serve as a cost-effective substitute for aggregates.
- Hauling and Disposal Fees: Instead of paying to transport concrete waste to a landfill, you can crush it directly on-site for reuse.
2. Environmental Sustainability
Concrete recycling helps reduce the environmental footprint of construction and demolition projects:
- Landfill Reduction: Crushed concrete takes up less space in landfills, freeing up capacity for other waste.
- Raw Material Conservation: Recycling concrete reduces the need for virgin materials, preserving natural resources like limestone and gravel.
- Lower Carbon Emissions: Producing recycled concrete requires less energy compared to mining and transporting new aggregates.
3. Versatility
Crushed concrete can be used in a variety of applications, including:
- Road Base and Subgrade Materials: Its stability makes it a popular choice for road construction.
- Drainage Systems: Crushed concrete provides excellent drainage for retaining walls, landscaping, and pipe bedding.
- New Concrete Production: When properly processed, recycled concrete can be incorporated into new concrete mixes.
4. Job Site Efficiency
Portable crushers, like the Rebel Crusher, allow you to process concrete directly at the job site. This eliminates the need for transporting material to a separate processing facility, saving time and resources while boosting productivity.
By crushing and reusing concrete, you’re not just managing waste—you’re creating opportunities to save money, reduce your impact on the environment, and streamline your projects. It’s a smarter, more sustainable way to approach construction and demolition.
How Does Concrete Crushing Work?
Concrete crushing may sound complex, but the process is straightforward when you have the right equipment. Here’s a step-by-step look at how it works:
Step 1: Breaking Down Large Concrete Pieces
Concrete demolition often leaves behind slabs, chunks, or blocks that are too large to use as-is. The first step is breaking these down into smaller, more manageable pieces. This may involve using hydraulic breakers, hammers, or other tools to prepare the material for the crusher.
Step 2: Feeding the Crusher
Once the concrete is broken into smaller pieces, it’s fed into a crusher. Crushers come in various types, each designed for specific applications:
- Jaw Crushers: These are ideal for primary crushing, breaking down large slabs into smaller chunks.
- Impact Crushers: Used for secondary crushing, they process concrete into finer, more uniform sizes.
- Hybrid Crushers (e.g., Rebel Crusher): Versatile machines that can switch between jaw and impact crushing modes, depending on the material and desired output.
Step 3: Separating Materials
Concrete often contains reinforcing steel (rebar) or other contaminants. Modern crushers are equipped with magnets or screens to remove these materials during the crushing process, ensuring the final product is clean and usable.
Step 4: Producing Reusable Aggregates
After processing, the crushed concrete is sorted by size and quality. These aggregates can then be repurposed for various applications, such as road base, backfill, or even new concrete production.
Step 5: Transport or On-Site Use
Depending on the project, the recycled concrete may be transported to a new location or used directly at the job site. Portable crushers like the Rebel Crusher make on-site crushing efficient and cost-effective, eliminating the need for additional hauling.
Concrete crushing is a simple but transformative process that turns waste into a valuable resource. By understanding how it works, you can unlock the full potential of recycled concrete for your projects.
Choosing the Right Crusher
Not all crushers are created equal, and selecting the right one can make or break your project’s efficiency. The right crusher depends on the size of your job, the type of material you’re working with, and your desired end product. Here’s a breakdown to help you make an informed decision:
Types of Crushers
Jaw Crushers
- Best For: Primary crushing of larger concrete pieces.
- How They Work: Use compressive force to crush materials between a stationary and a moving jaw.
- Advantages: Simple design, durable, and capable of handling tough materials like reinforced concrete.
Impact Crushers
- Best For: Producing finer materials or achieving a more uniform product size.
- How They Work: Use high-speed rotors to hurl concrete against hard surfaces, breaking it down through impact.
- Advantages: Efficient for secondary crushing and ideal for creating aggregates for road base or drainage systems.
Hybrid Crushers (e.g., Rebel Crusher)
- Best For: Projects requiring versatility and portability.
- How They Work: Can function as both a jaw or impact crusher, adapting to various materials and output needs.
- Advantages: Combines the benefits of jaw or impact crushers, making it a cost-effective choice for diverse jobs.
Key Factors to Consider
1. Project Size and Volume:
- For small to mid-scale jobs, portable crushers like the Rebel Crusher are ideal.
- Large operations may benefit from high-capacity stationary crushers.
2. Material Type:
- Concrete with heavy rebar may require a robust jaw crusher.
- Softer or more uniform materials are well-suited for impact crushers.
3. Mobility Needs:
- If you need to process materials at multiple sites, a portable crusher ensures efficiency and reduces hauling costs.
4. Desired Output:
- Consider the size and shape of the crushed concrete you need. Impact crushers are better for finer aggregates, while jaw crushers are ideal for bulk material.
5. Ease of Use and Maintenance:
- Look for user-friendly features like quick setup, accessible wear parts, and minimal maintenance requirements.
Rebel Crusher: The Ultimate Crushing Solution
When it comes to concrete crushing, the Rebel Crusher is a standout solution, combining power, versatility, and ease of use into one machine. Whether you’re a contractor tackling small demolition projects or managing large-scale material processing, the Rebel Crusher has features that meet your needs.
Unmatched Versatility
The Rebel Crusher adapts to a variety of applications, making it ideal for crushing:
- Concrete
- Asphalt
- Rock
- Brick
- Granite
- Other materials like glass or block
Its ability to function as both a jaw or an impact crusher allows it to handle diverse materials and output requirements, giving you more flexibility on the job.
Portable and Efficient
Designed with mobility in mind, the Rebel Crusher can be easily transported to different job sites, eliminating the need for extensive hauling. With a quick setup time and self-contained diesel, you can hit the ground running without relying on external power sources.
Key Features
- Magnet for Steel Removal: Effortlessly separates rebar and other metals during crushing.
- Fuel Efficiency: Engineered for lower operating costs and a smaller environmental footprint.
- Compact Design: Despite its power, the Rebel Crusher is easy to maneuver and operate.
- User-Friendly Interface: Simple controls make it accessible for operators of all skill levels.
Why Choose the Rebel Crusher?
Unlike traditional crushers, the Rebel Crusher is built for adaptability. It’s a one-stop solution for contractors and businesses looking to maximize efficiency and minimize costs. By choosing the Rebel Crusher, you’re not just investing in equipment—you’re investing in smarter, more sustainable operations.
Common Myths About Concrete Crushers
Concrete crushers play a vital role in transforming demolition waste into reusable materials, but misconceptions about them often deter people from realizing their full potential. Let’s debunk some common myths and set the record straight:
Myth 1: Crushing Concrete Is Too Complicated
Many believe that concrete crushing requires advanced expertise or complicated equipment. In reality, modern crushers, like the Rebel Crusher, are designed to be user-friendly, with intuitive controls and straightforward maintenance. Whether you’re a seasoned professional or new to crushing, today’s technology makes the process accessible for all.
Myth 2: Crushers Are Only for Large-Scale Operations
While some crushers are built for massive construction projects, portable models have made concrete crushing viable for smaller contractors, landscapers, and even DIY enthusiasts. Compact crushers can easily handle jobs like driveway reconstruction or repurposing old slabs into useful materials without the need for heavy-duty infrastructure.
Myth 3: All Concrete Crushers Are the Same
Not all crushers are created equal. Some are tailored for primary crushing, while others are designed for specific materials or finer outputs. For example:
- Jaw crushers are ideal for breaking down large chunks of concrete.
- Impact crushers excel at producing uniform, high-quality aggregates.
- Hybrid crushers, like the Rebel Crusher, combine multiple capabilities into one machine, offering unmatched versatility.
Myth 4: Concrete Crushing Isn’t Cost-Effective
Many assume that concrete crushing is expensive compared to disposing of debris in landfills. However, crushing concrete on-site can save money by:
- Reducing hauling and disposal fees.
- Providing affordable, reusable materials for future projects.
- Minimizing the need to purchase new aggregates.
Myth 5: Recycled Concrete is Inferior
Another common misconception is that recycled concrete lacks the strength or durability of new materials. In truth, when properly processed, crushed concrete performs just as well as virgin aggregates in many applications, including road base, drainage, and backfill.
Breaking Through the Myths
Concrete crushing has come a long way, and the advancements in equipment and techniques make it a smart, sustainable option for projects of all sizes. By understanding the truth behind these myths, you can unlock the full potential of concrete recycling and make informed decisions for your business.
Tips for Maximizing Crushing Efficiency
Concrete crushing can be a highly efficient process, but achieving optimal results requires the right preparation, techniques, and maintenance. Follow these tips to make the most of your crushing operations:
1. Prepare the Material Properly
Before feeding concrete into a crusher, take steps to ensure it’s ready for processing:
- Remove Contaminants: Strip away rebar, wires, or other non-concrete materials that could damage the crusher or reduce the quality of the final product.
- Break Down Large Pieces: Use hammers or breakers to reduce oversized chunks, making it easier for the crusher to handle them.
2. Choose the Right Crusher Settings
Adjusting your crusher settings can significantly impact the quality and consistency of your crushed material:
- Output Size: Select the appropriate screen size to achieve the desired aggregate size for your application.
- Feed Rate: Avoid overloading the crusher by maintaining a steady feed rate, which ensures consistent performance and prevents wear.
3. Maintain Equipment Regularly
Proper maintenance not only extends the life of your crusher but also improves efficiency:
- Inspect Wear Parts: Check for wear and replace components like blow bars, jaw plates, and screens as needed.
- Lubricate Moving Parts: Keep all moving parts well-lubricated to minimize friction and prevent breakdowns.
- Clean the Crusher: Remove debris and buildup to maintain optimal functionality.
4. Optimize Material Flow
Efficient material flow minimizes bottlenecks and boosts productivity:
- Use Feeders and Conveyors: Feeders and conveyors help regulate material input, ensuring a smooth and consistent feed.
- Position the Crusher Strategically: Place the crusher close to the demolition site or material pile to reduce transport time and costs.
5. Train Your Operators
Even the best equipment requires skilled operators to get the job done right:
- Provide Training: Ensure your team understands how to use and maintain the crusher safely and efficiently.
- Monitor Performance: Regularly evaluate operations to identify areas for improvement.
The Payoff: Better Results and Lower Costs
By following these tips, you can maximize the efficiency of your crushing operations, reduce downtime, and produce high-quality aggregates. Whether you’re using a portable crusher like the Rebel Crusher or a more traditional setup, optimizing your processes will ensure you get the best return on your investment.
Why R.R. Equipment Is Your Crushing Partner
Concrete crushing is more than just a process—it’s a crucial step in turning waste into opportunity. But to do it effectively, you need the right equipment and a trusted partner by your side. That’s where R.R. Equipment comes in.
Experience You Can Count On
With over 50 years in the material handling industry, R.R. Equipment has the expertise to help you tackle any project. Whether you’re crushing concrete, asphalt, or rock, we understand the challenges and know how to deliver solutions that work.
Innovative, Patented Products
R.R. Equipment is proud to offer cutting-edge machinery like the Rebel Crusher, which combines versatility, efficiency, and ease of use into one revolutionary product. Our equipment is designed to:
- Handle a variety of materials with precision.
- Maximize productivity on job sites of any size.
- Deliver consistent results with minimal maintenance.
Customer-Focused Solutions
At R.R. Equipment, our goal is to make your job easier. We provide:
- Customizable Options: Choose equipment tailored to your specific needs, whether it’s portability, capacity, or output size.
- Exceptional Support: From initial consultations to ongoing maintenance, we’re here to support you every step of the way.
- Parts Availability: Keep your operations running smoothly with our reliable parts inventory and quick delivery.
Sustainability at the Core
Recycling is at the heart of what we do. By helping our customers repurpose materials through innovative crushing solutions, we’re collectively reducing landfill waste and conserving natural resources.
Join the R.R. Equipment Family
Choosing R.R. Equipment means choosing a partner committed to your success. Our team is here to guide you through the process, from selecting the right equipment to ensuring your projects run smoothly. With decades of experience, innovative products, and customer-first service, we’re the trusted name in concrete crushing and material handling.
Let us help you crush your goals. Contact R.R. Equipment today to learn more about our products and services!