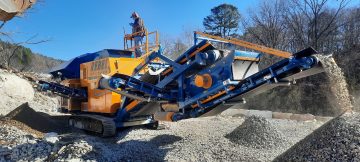
Fact number 1: If it was EASY, everyone would be doing it. Don’t be fooled. It’s not as easy as salesmen say it is. Crushing concrete, crushing rock, and crushing asphalt has its challenges. When done right, the profits can be HUGE. Know the facts and understand as much about your particular and regional challenges before entering into the business.
Fact number 2: Know your competitors and their prices. Do research to see what crushed concrete is selling for at the site and delivered. Pricing fluctuates significantly depending on where you are located. In addition, do you know what the local sand and gravel mine or rock quarry is selling stone for? They may be a competitor who you should be aware of.
Fact number 3: Try to understand the demand for crushed concrete in your area. Are there any other sources of material and/or suppliers that may compete with you? Try to determine the overall volume of material currently being sold in your area. If you got into the business of crushing concrete and recycled material, what volume of material could you sell? The demand for crushed concrete can and will fluctuate, thus the reason the machinery you have should be versatile and able to produce various sizes as the demand dictates.
Fact number 4: Know what size material is in demand. Understanding the size of the material that people will want and buy from you is critical. Having a machine that can produce a variety of materials “on the fly” has massive advantages. Not knowing what the future holds, one must have the ability to produce the size material that is in demand today and tomorrow.
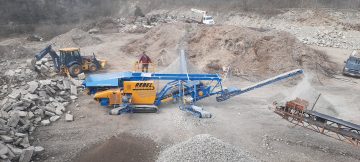
Fact number 5: Various size materials can be priced differently. You should be rewarded for being able to supply perfectly screened and sized materials. Base material ( 1 1/2″ minus) may be sold and priced less than clean 3/4″, for example. Similarly, clean 3/8″ may be worth more than 2″ clean. Screening your crushed concrete and crushed stone will pay dividends because you can charge more when the product is screened and refined. In addition, you should sell more volume quicker because you are able to produce exactly what is in demand at the time. The screening system is a vital feature of your concrete crushing operation.
Fact number 6: The gradation of the material you produce will affect the quality of the product and possibly the demand for your product. Knowing if you require a higher percentage of fines or coarse material is critical. You want to produce the best product quality that will help you to sell your material quickly and for the most money. Understanding the gradation of material is vital. Sometimes, certain states have specific gradation requirements to meet a DOT specification. Did you know the REBEL CRUSHER JAW has hit the CALIFORNIA DOT specification for crushed concrete? It can produce a beautiful blend of material with a perfect amount of fines and coarse material that is below 1″.
Fact number 7: Continuing off of fact 6, the gradation may be important for compaction. Having the correct percentages of different sizes can be critical in meeting a compaction specification. Not all crushed material is compactible. However, the REBEL CRUSHER will give you the best chance of meeting whatever the compaction codes are because its onboard screening system can be easily adjusted to meet the codes.
Fact number 8: We’ve talked a great deal about the finished products and the size of the crushed concrete. We would be remiss if we did not mention how raw and large chunks of concrete and asphalt are prepared BEFORE loading into a REBEL CRUSHER. Depending on the size of the raw feed material, it may be necessary to prepare the feed material with a hydraulic hammer, concrete cruncher or concrete pulverizer. Various concrete and asphalt preparation attachments have pros and cons. For example, hydraulic hammers are readily available and come in a wide assortment of sizes and shapes. Hydraulic hammers have a focused point and can apply maximum pressure to break hard material. However, the hydraulic hammer can be a slower process because it has a point and not teeth. A concrete cruncher or concrete pulverizer have a larger surface area and can process slabs quicker. The downside is that concrete crunchers and concrete pulverizers may not have the same ability as the hydraulic hammer to break very hard material. Selecting the proper concrete crushing attachment will enable you to have the most cost effective and efficient concrete crushing operation.
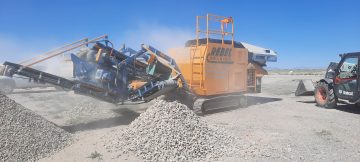
Fact number 9: Number of operators and/or employees on a jobsite. Obviously, the more employees and more operators you have will increase your jobsite investment and hourly costs of crushing concrete, crushing asphalt and crushing rock. Having simple crushing solutions with minimal operators can not only be efficient, it will save you a great deal of money. The REBEL CRUSHER, for example, can be a one man operation. The loader operator can keep the radio remote control inside the loader cab while feeding the REBEL CRUSHER and loading trucks. Keeping your labor to a minimum in any operation is a critical consideration.
Fact number 10: Machinery required to get the job done. Knowing the overall size and scope of your operation is vital. Having the right sized machinery size and matching the amount of ancillary equipment to support the machinery allows you to maximize profit and complete each project in your desired timeframe. Your overall jobsite investment includes the concrete crusher and screen as well as the employees, preparatory equipment, loading equipment and anything that you require to get the job done. All of these machines should be considered and utilized as required with a focus on minimization.
Fact number 11: Dust and environmental concerns must be considered when crushing concrete. Various regulations may exist depending on your location, state or region. Dust can be controlled and minimized to prevent you from being environmentally unfriendly. One of the best ways to minimize dust creation is to select the style of crusher that produces the least amount of dust. Jaw crushers operate at slower speeds and compact/squeeze material while producing a minimum amount of dust into the atmosphere. Impact crushers operate at higher speeds and produce a significant amount of dust into the atmosphere. Yes, the dust can be controlled to an extent. However, more dust suppression measures must be taken when operating an impact crusher. See our other posts on the pros and cons of operating a jaw crusher vs an impact crusher.
Fact number 12: Jobsite noise can be a consideration depending on where you are crushing concrete, asphalt or rock. Knowing the decibel readings that are acceptable in the area you’re working in, is important. The Rebel Crusher averages about 70 decibels from 50 feet away. The REBEL CRUSHER is designed to minimize noise creation and work in a city environment without negatively affecting the general area it’s working in. Jaw crushers tend to produce less noise and are more readily accepted in crowded and tight city atmospheres.
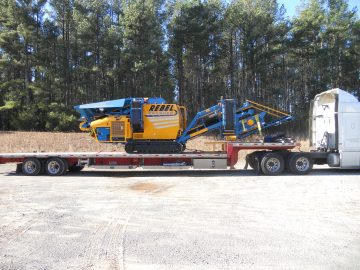
Fact number 13: Consider machinery mobility. When selecting the proper equipment one must consider how easily it can be transported and if any transport permits are required. It can take days if not weeks to obtain some transport permits. In addition, some sites may be inaccessible for equipment that is too heavy or large to go over bridges and certain roadways. Having machinery such as the REBEL CRUSHER that is big enough to get the job done but mobile enough to get in and out without transport permits is critical and can be the defining reason you can do the job. Once onsite, the mobility of the crusher in and around the jobsite will help you to go where the input material is and move as required.
Fact number 14: Concrete hardness and steel embedded in the concrete. Not all waste concrete is created equal. There is wash out, sidewalk, residential concrete, as well as factory floor concrete and concrete footings. Various types of concrete have various ingredients including rebar, wire, type of rock, percentage of sand, etc. The harder the rock in the concrete, the harder it is to crush and the more wear on your machine. In addition some concrete can be more abrasive than others. The amount of rebar, steel and wire in the concrete will also affect the wear parts adversely. Having a machine such as the REBEL CRUSHER JAW, will give the maximum advantage of processing this material properly and with a minimal amount of wear and tear. The finished crushed concrete quality will also be affected by the input and type of material being fed. Wash out concrete will most likely have a higher percentage of fines and not be as good of a rock substitute as factory floor concrete.
Fact number 15: We have provided some of the top 15 items to consider when crushing concrete. Thes provided concrete crushing FAQs are generic and provide an overall picture of most of the considerations but not all. To get a more comprehensive understanding of everything you should consider, please review all of our posts and consult one of our factory sales representatives. Please visit us at www.rrequipment.com.