Rock quarries, sand and gravel operations, concrete and asphalt recyclers all utilize similar screening methods. There are a variety of styles of screen systems depending on the application.
The most common styles of screens are inclined vibratory screens. This style of screen is shaped like a shoe box and can have one level or multiple levels. Each level separates material as it passes over the screen media.
The overall screen sits on springs that allow the screen box to vibrate. The screen box will have some type of vibratory mechanism that is either electrically or hydraulically powered. The mechanism is attached to the box and will create a vibration that most likely shakes the screen box while moving the material forward.
Material is fed onto the screen by a feeder or conveyor or possibly directly by a crusher. The feed material is fed onto one end and shakes down the screen and over the screen media as it travels towards the discharge end. Material that passes through the top deck screen media will either be discharged or falls onto the next level of screen media.
For example, let’s say we have a three-level screen and want to produce four different size rocks. If the top deck is 2″, second level 1″ and bottom level 1/2″ then four products can be made at the same time providing the feed material is approximately 3″ minus rocks. As the 3″ minus rocks shake down the screen, all material that is over 3″ will discharge off the top deck into a chute. Material that passes through the top deck but does not pass the second deck is the next product and most likely material that is less than 2″ and larger than 1″. The same goes for the next level until all material that passes through all three levels is discharged as 1/2″ minus (includes fines).
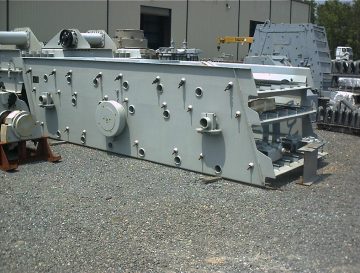
Screen media can be made from a variety of material and comes in different configurations. Woven steel wire is most common. There is also laser cut steel plates, grizzly bars, urethane and rubber materials. Each type of material can have different size openings and thickness of spacings as well as wire diameters.
Various material, wire diameters and openings are utilized depending on the type of material to be screened and other considerations. Screen cloth is another name for screen media. The screen media can be changed or replaced. it is normally wedged in and comes in 1-4 panels per deck. Smaller replaceable panels are easier to handle and allow operators to reduce costs by only changing the panel that is worn rather than the entire length of the screen level.
Screen boxes can be inclined, horizontal or cylindrical (trommel) in shape. Each shape and style have pros and cons. As stated, the most common is inclined and mostly used in normal rock crushing and screening applications. Inclined screens are less expensive to purchase, versatile and require less horsepower to operate by incorporating gravity to move material across the screen media.
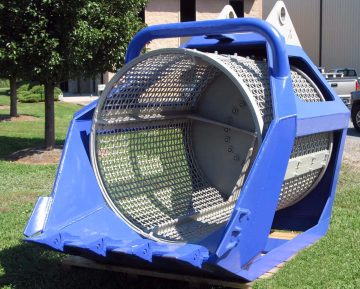
Horizontal screens allow material to stay on the screen media for a longer period of time and require more horsepower to operate. When material is more difficult to screen of may require washing, horizontal screen can have advantages. In addition, horizontal screens may be able to fit into tighter spaces when space is limited. They are normally mor expensive to purchase.
Trommel screens (rotating screens) will tumble material and have advantages in topsoil and various sand applications. Depending on the material and what it consists of various screen styles will be utilized to achieve maximum results and efficiency. Trommel screens have more expensive screen media and media is normally pre-curved by screen media manufacturers. Although some screens can be shaped to contour to the curve when they are installed.
There are more specific screens and specialized systems for unique rock applications. The big three are inclined, horizontal and trommel screens.
For contractors and more mobile operations, screens can be mounted on portable chassis or track-mounted. Track-mounted systems can be advantageous when maximum jobsite mobility is desired.
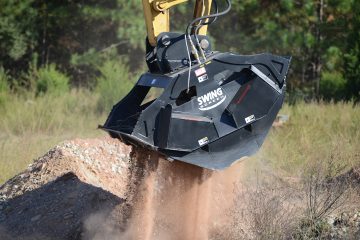
Screening systems are normally paired and follow crushing operations. Once the material is crushed, it is introduced onto the screen to be separated. In addition, material that does not pass through a screen can be recirculated back to the crusher. This is known as a closed-circuit system.
Screens can be used to screen rock, concrete, asphalt, bricks, glass and a variety of materials that are hard and require screening. Various screens are used in recycling glass and plastic and can remove soil or dirt that may be mixed with the glass or plastic.
Keep in mind that this is an overview and meant to be brief. Therefore, the last thing is the size of the overall screen box. The larger the screen box the more production it is capable of effectively screening. Screens that are larger have more surface area per deck/level and allow for maximum efficient results.
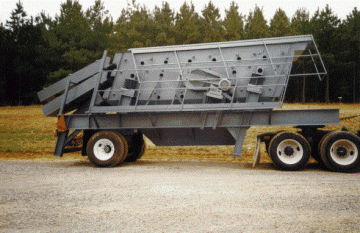
In addition to the size of the screen box, some screens are considered high frequency or simply shake with more violence or with more throw. In some applications where surface area is not critical a high frequency screen or one that shakes more violently can have advantages.
Its’ all about the type of material and what you want to achieve. Common vibratory screens may not work in all applications thus the reason there are alternatives.
Rock quarries know the value of screens and typically will place a screen in between each crusher. If the quarry has four crushers, 3-4 screens may be utilized to screen out any material that does not require crushing. Since screening rocks is less expensive than crushing rocks, the rule of thumb is not to crush anything you don’t have to. Screens eliminate the need to have material crushed by screening out the desired size and discharging the material prior to the crusher.