The jaw crusher and the impact crusher are both popular. There are pros and cons associated with running and maintaining either one. It is most important to choose the correct type of crusher based on what you intend to do with it. What type of material do you plan to crush? How big is the material you plan on crushing and feeding into the crusher? How small do you want to crush the material down to? Do you think you will ever crush other types of materials? Do you require a certain gradation or DOT code with the crushed material? In addition, to the most common factors in determining what type of crusher, there are other considerations such as: gradation of input material, moisture content, abrasion considerations, hardness, amount of preparation necessary to reduce huge chunks into a more manageable size to feed the crusher, mud, fines, steel, rebar, contaminants, dust creation, dust and fines in the finished product, etc.
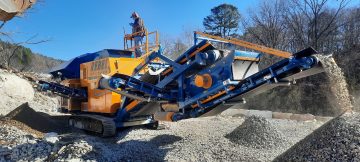
The most popular and versatile crusher is a JAW crusher. Impact crushers and Cone crushers are second and third in popularity. The jaw crusher is not perfect even though it is popular. Its popularity stems from a variety of factors. In general, the jaw is considered a more rugged and durable crusher. Jaw crushers are often used when material is very hard, such as granite. Jaw crushers operate at low speeds and tend to require less horsepower to operate. Jaw crushers have replaceable wear plates. Jaw crushers can be adjusted to produce a variety of discharge sizes. Jaw crushers are typically less noisy and create less dust in the atmosphere and in the finished discharged product.
Most jaw crushers can accept large chunks of hard material and reduce the material to a small to medium discharge size. On average, a jaw crusher reduces material at a 5 to 1 ratio.
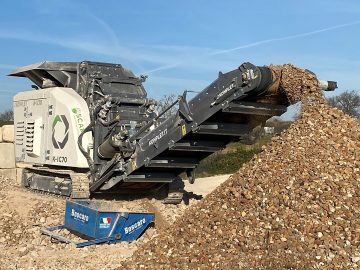
Impact crushers are mostly used in softer material applications. However, soft could mean concrete with or without rebar, asphalt and limestone. There are a variety of impact crusher designs and one must understand the complexity of choosing the correct design. There are primary as well as secondary designs. There are “Andreas” styles as well as various rotor designs. One must choose the proper rotor diameter and the number of “blow” bars per rotor. One must consider a range of rotor RPM as well as the type of blow bar materials. In essence, there are many more considerations when selecting the proper impact crusher.
Impact crushers can accept larger chunks of medium to soft hardness materials and reduce the material to very small, small or medium discharge sizes. On average, an impact crusher can reduce material at a 8 or 10 to 1 reduction ratio. If your goal is to produce a higher percentage of powder and dust in the discharged material, the impact crusher should be considered.
Talking about the most common pros and cons, one must consider the horsepower required, noise, dust, cost and frequency of replacement of the wear parts, general maintenance costs as well as the initial cost to purchase the machine. Again, your specific application will dictate the type of crusher you should use. On average, jaw crushers require less HP, produce less dust, are less noisy, the cost of wear parts replacement and maintenance is less than an impact crusher; general maintenance and cost to purchase are similar for jaws and impacts. However, the impact crusher may have less expensive wear parts but may require more frequent replacement. One must consider the labor and time to replace wear parts more frequently regardless of the cost of the wear parts.
You should speak with one of our experts to be sure you are selecting the correct style of crusher. There are specific reasons that jaw crushers as well as impact crushers are designed and built. If one design would do it all, there would not be a wide variety of designs, styles and/or types of crushers.
At R.R. Equipment Company we strive to offer a wide variety of crushers and screens in order to meet the needs of our customers who have a variety of applications.
Give us a call to discuss your application at (803) 416-5200 or email us at sales@rrequipment.com
We look forward to speaking with you.