Some may ask, “WHAT IS A CRUSHER OR STONE CRUSHER USED FOR?”
The SHORT Answer: A rock crusher is used to reduce large rocks in order to use the reduced rocks in various applications.
This post will explore the purpose of crushers, focusing on rock crushers, how they function, and why they are essential in various industries like mining and construction. We’ll also discuss the different types of rock crushers and how they operate.
WHY would anyone want to crush rocks?
Rocks are used in numerous applications and are considered the building blocks of all construction. Did you know that there are rocks in concrete? Did you know there are rocks in Asphalt, bricks, cinder blocks, pavers and sheet ROCK? Rock crushers are used to reduce the size of large rocks into a more desirable size so the rocks can be used in the previously mentioned applications. Rocks in concrete can have various sizes depending on the desired mix and hardness of the concrete. Similarly, in asphalt, rocks may be of various sizes depending on the desired specifications of the asphalt.
Smaller rocks may be more desirable in concrete or asphalt when the finish coat is being smoothed out by pavers or rollers. Larger rocks may be embedded in the concrete or asphalt and used as fill material below the finish coat of concrete or asphalt. The larger rocks may provide a harder consistency and thus having the rocks embedded in the asphalt or concrete will add strength to the concrete similar to reinforcement.
The Primary Purpose of a Rock Crusher
The rock crusher is therefore used to reduce various rocks or stones into sizes to be further used in materials that are man made. The natural rocks or natural stones act as part of the mixture to enhance the strength and consistency for the man made materials such as concrete or asphalt. Similar to ingredients in a recipe for a cake, the rocks in concrete could be analogous to eggs in a cake. The rocks add strength, cohesion and consistency to concrete, asphalt bricks and the like.
HOW DO CRUSHERS WORK?
It depends on the particular style of crusher. There are various methodologies based on numerous factors, including but not limited to type of rock, size of input material, size of desired output, gradation of desired output, etc. We will discuss the different types of crushers later in this article.
Understanding Reduction Ratios:
It is industry standard to have each crusher perform an approximate 5 to 1 reduction to maximize efficiency and by allowing each machine to share in the work. A rock crusher has limitations. Rock quarries understand that crushing is a “team” effort. Each crusher(player) is essential and serves a specific purpose. Just like no one player can be a baseball team, no one crusher can do it all.
Rock crushers reduce rocks into various sizes but can also transform the shape of the rocks to be more desirable. For example, there are rock crushers designed to produce a more cubical product if that is what is required. There are rock crushers designed to produce sharper edges if that is what is desired. There are primary crushers, secondary crushers, tertiary crushers, etc. that are all designed for different applications. The design of the rock or stone crusher is specific to the size and hardness of the input material In addition, the design of the rock or stone crusher can affect the size of the material being discharged.
Understanding the Importance of the Rock Crusher Design
Rock crushers can also be used to vary the gradation of the discharged material. Graduation is defined by the percentage of various sizes. Different rock crusher designs can and will affect the gradation and/or percentage of fines and coarse material. The design of an impact crusher, for example, may contribute to the discharged material having a higher percentage of fines, powder and sand. The impact rock crusher, therefore, could not only be used to produce smaller rocks but also used to produce a change in gradation.
A BASIC Process for crushing rocks:
STEP 1:
A rock quarry may start the process by drilling and blasting natural rock formations. The spacing of the drill holes, diameter of the drill holes, depth of the drill holes and the actual amount of dynamite in each hole will produce the specific desired results.
Once material is blasted it may be necessary to further reduce any large chunks that remain. There are various ways to reduce the large chunks including hydraulic hammers or drop balls and drop crosses.
STEP 2:
Once material is processed it is ready to be fed into the rock crusher primary. The primary crusher is most often a jaw crusher with a large feed opening. The jaw is a heavy duty crusher that is specifically designed to reduce the large chunks into a more manageable size to be further reduced by a series of smaller secondary and or tertiary crushers.
STEP 3:
Prior to the primary crusher and in between each crusher would most often be a screening system. The concept of screening prior to each crusher is to maximize production while reducing wear and tear on crusher wear parts. By screening prior to each crusher, it ensures that the only rocks that go into the crusher are rocks that require crushing.
The screening systems can be multiple layers or decks and can have a variety of screen media installed to achieve the desired rock sizes. The desired rock sizes are then conveyed into stock piles to be loaded on trucks and delivered to prospective clients or job sites.
STEP 4:
The material that was crushed by the primary crusher and does not pass through the top deck screen of the screen positioned after the primary could go to the secondary crusher to be further reduced. The secondary crusher could be a cone crusher or an impact crusher in most quarries. The secondary crusher will most likely produce material through a 5 to 1 reduction ratio and contribute to the second process of crushing the rocks. If the rocks are hard and abrasive the cone crusher may be better suited. If the material and/or rocks are softer or less abrasive an impact crusher may be utilized. Again, the goal is for each crusher to do a little bit of the work and the team effort produces the desired results without creating too much stress on any one crusher. The cone vs the impact crusher may also produce a different gradation or material due to the methodology of the cone crushing mechanism vs the methodology of the impact crusher.
STEP 5:
Once again, a screening system would be placed after the secondary crusher to separate crushed rock into various desired sizes. Any material that does not pass the top deck of this screen could go on to tertiary crusher to be further reduced.
STEP 6:
The process goes on and on depending on the size of the quarry and the overall desired production rate. Massive quarries may have a dozen crushers and screen with each machine sharing in the workload. The overall idea is to screen then crush then screen then crush then screen, etc. etc. In between each screen there will be conveyors positioned to stockpile desired finished products that have passed through the appropriate size screen media.
This is a simplistic overall explanation that will vary for each quarry operation. Please contact us for assistance or a more detailed explanation.
Most Common Types of Rock Crushers
There are various types of crushers, including jaw crushers, cone crushers, and impact crushers. Each type of crusher has its specific use case depending on the material being crushed and the desired size of the output. For an in-depth review of each type of crusher, read our article about the different types of crushers.
Jaw Crushers
Jaw crushers are the most versatile machines due to their ability to crush nearly any type of material including but not limited to rocks, sand and gravel, concrete with rebar, asphalt, bricks, blocks, glass, ceramics, etc. Traditional jaw crushers produce less dust in the discharge material as well as the atmosphere. In the case of the US patented Rebel crusher Jaw, it has maximum versatility by being able to crush nearly anything in one pass into a desirable size.
Impact Crushers
Impact crushers are more specific application machines. They are less popular mostly due to the smaller input size of the rocks, the rocks should be softer and the more frequent replacing of wear parts. They have their place in the industry when input material is softer and/or the desired output material is dust, fines or very small.
Impact crushers operate at high speed and explode material that falls onto a high speed spinning rotor. This crushing action achieves maximum results when material is soft, spongy and smaller in input size.
Cone Crushers
Cone crushers are secondary crushers that typically follow a primary crusher such as a jaw crusher. Cone crushers are used to further reduce material that has already been crushed by a primary crusher or is naturally small in size. Having a desired 5 to 1 reduction, cones can be used similar to jaws in crushing similar material. Cones are rugged, slower speed and are capable of efficiently crushing smaller material into even smaller more desirable sizes.
Again, this is a short and simple explanation of the three most popular crushers. There are numerous factors to take into consideration when choosing the appropriate style of crusher. We’ll be happy to discuss the proper application of each machine in more detail anytime.
In addition to jaws, impacts and cones, there are hammermills, ball mills, roll crushers and a variety of unique styles that are less popular.
The Importance of Rock Crushers in Today’s Industry
Rock crushers are indispensable tools that transform raw, bulky rocks into various sizes essential for construction, manufacturing and infrastructure projects. From roads and highways, to building foundations and bridges, crushed rock forms the backbone of many different applications. By selecting the appropriate crusher and implementing each step in the crushing process efficiently, you can maximize production while meeting specific project requirements.
As demand for crushed materials grows, understanding the role and functionality of each crusher type becomes more crucial. Whether you’re creating asphalt or researching how to start a profitable crushing business, choosing the right equipment and method for rock reduction is key to achieving strength, durability and consistency.
Contact us today if you have any questions about purchasing or using a rock crusher.
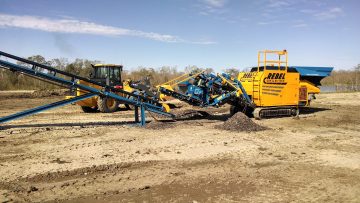
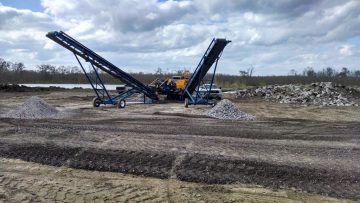